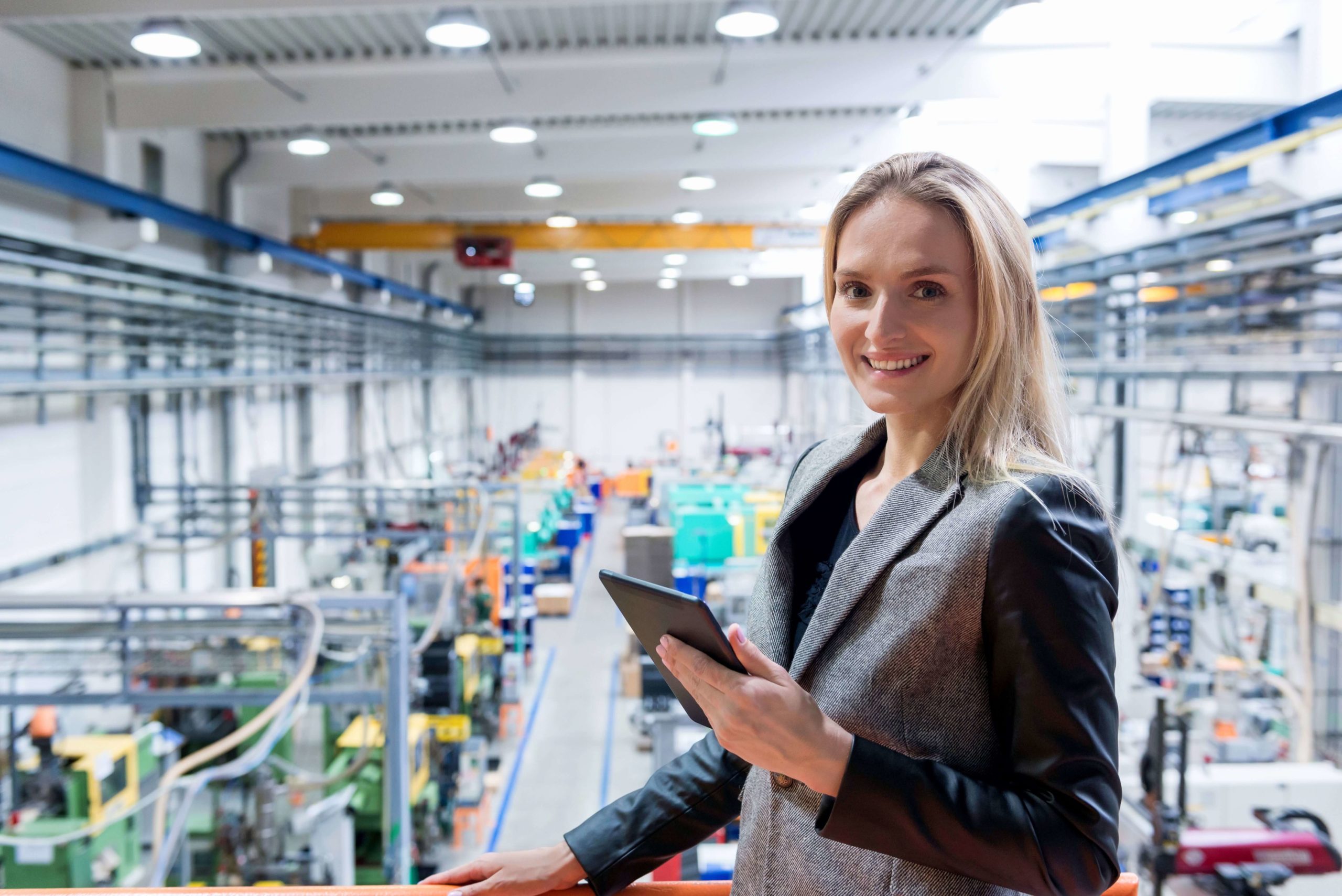
Last Updated: 17 Jul 2020 5S in the Japanese workplace – sorting out seiri (part 1 of 5)
A common source of frustration for Japanese supervisors
For over 25 years, at Japan Intercultural Consulting we have been helping Japanese supervisors and managers working in the U.S. gain the skills they need to become effective leaders. Here is a common challenge.
Morimoto has recently been assigned to work as a coordinator at one of his company’s factories in the U.S. The first time he walks into the factory, he is shocked to see tools piled in corners and a trash can filled with old takeout containers. He is dismayed by the way the Americans work. Don’t they know about 5S practices? When he asks about them, he is shown a line of white tape in front of one of the machines. The tape makes no sense. It is not in the right place. Since Morimoto doesn’t know the best way to communicate his expectations he says nothing, but inside he is frustrated and irritated.
Why the Japanese have difficulty explaining 5S
Most American managers and workers know something about 5S. A Google search will find multiple variations of the definitions of the five concepts, sometimes Seiri = sorting, Seiton = organizing, Seiso = cleaning, Seiketsu = sanitizing and Shitsuke = sustaining. Other times Seiri = organizing or clearing up or ordering. How confusing! The top search results are consultants to help roll out 5S programs and manufacturers of tags and labels. A search of the history of 5S traces it back to the 1950s, a time when the Japanese were refining their innovative lean manufacturing systems.
It is important to know the cultural roots of 5S
In order to work more effectively with the Japanese, it is important to have a deeper knowledge of these five concepts and how they relate to 5S initiatives. This will enable you to not only meet the Japanese expectations in this regard but to proactively identify and eliminate sources of frustration and irritation.
5S—the basics
The following table shows the basic 5S definitions and activities. It is reproduced by permission from “製造現場の英語表現 (Seizo gemba no eigo hyogen) (Effective Communication for Engineers)” by Rochelle Kopp, which is a best seller in Japan. The book helps Japanese engineers use English effectively to communicate important information, including 5S.
日本語 |
英訳① |
英訳② |
英訳③ |
整理 |
Clearing up あるいはOrdering |
Separate the necessary and unnecessary items in the workplace. Remove the unnecessary. |
Straighten up – decide what you need. |
整頓 |
Organizing |
Set all necessary items in a neat orderly fashion so they can be located and retrieved safely and quickly. |
Store – everything in its place. |
清掃 |
Cleaning |
Shine and clean everything in order to spot hidden problems (oil leaks, water drops, etc.) |
Shine – clean it up. |
清潔 |
Sanitizing あるいはMaintaining Sanitary Conditions |
Scan your work area for outdated, poisonous and otherwise dangerous materials and remove them from the work area. |
Sanitize – make it safe. |
しつけ |
Training and Discipline |
Sustain and standardize the above four actions so that they become part of the daily routine. |
Strive – to compete these every day. |
.
Common 5S theme—space is precious
Most urban Japanese have learned to live in very confined spaces. For some families, the living room is also the dining room and is also the bedroom. During the day the bedding must be put away to make room for daytime activities. At night, the table and seats must be put away so that the bedding can be laid down. There is no room for unnecessary items or clutter. Items that are not in daily use must be stored efficiently or thrown away.
Common 5S theme—the importance of visuals
As a communications media, the Japanese rely on images as well as text. The popularity of white boards, PowerPoint images, visual aids used in television news, and even little cartoons in government publications speaks to the importance of visuals to supplement words.
Visual observation is also a key aspect of 5S. Every step requires taking another look at everyday items and practices. Many steps involve marking or labeling items and processes in a way that their state or purpose can be easily visually identified. Let’s look more closely at the 5S concepts, starting with Seiri.
Seiri—clearing up and ordering
A simple description of Seiri action is “Separate the necessary and unnecessary items in the workplace. Remove the unnecessary.”
Seiri-(整理)
The origin of the word goes back at least 2,500 years to the Chinese Confucian philosophers. “Ri”(理) is “harmony,” “order” and “morality.” Literally, “seiri” means “establishing ‘ri.’” Its opposite is “muri”(無理), or “non-ri,” wasted labor, unreasonableness and absurdity. In Japanese, the character for “ri” can also be pronounced “kotowari,” which means “separating out,” “rejecting” and “refusing.” Without separating and rejecting, order cannot be established.
Seiri—identifying what is unnecessary
Seiri involves taking a fresh look at the workplace and identifying unnecessary items. Clutter can pose a hazard on the work floor. Clutter makes it difficult to see the items that are needed for work. However, throwing away items, especially if they have potential value, is not that easy. Eliminating clutter requires the establishment of criteria for keeping or getting rid of items.
Seiri—identifying what is necessary
In order to know what is necessary, the purpose of the activity at hand must be clearly identified. This is where Japanese Buddhist thought comes into play. Keeping in mind “Do what you are doing and do not do what you are not doing” provides a basis for Seiri activity. This means coming to terms with the now and eliminating what is not now.
Seiri—rejecting and letting go
Identifying and eliminating unnecessary items means giving up illusions and letting go of possibilities. An example is getting rid of tools purchased for producing a product that is not needed in the marketplace. It also means giving up on failures. An example is getting rid of parts left over from a project that failed miserably. Seiri means denying the possibilities of “we might need that someday” and accepting that we won’t.
Seiri— observing, identifying, separating and rejecting—and keeping.
Related articles
Purpose should come from within, but also from outside Japan HQ
Recently an HR director for a Japanese financial services company in Europe told me that he had been
(Video) So, What is Monozukuri Actually?
Monozukuri is one of those well-known and often used Japanese words among people from outside of Jap
(Video) So, What is Ikigai Actually?
Ikigai - The Japanese word for the goal that gets you going - is often misunderstood by non-Japanese