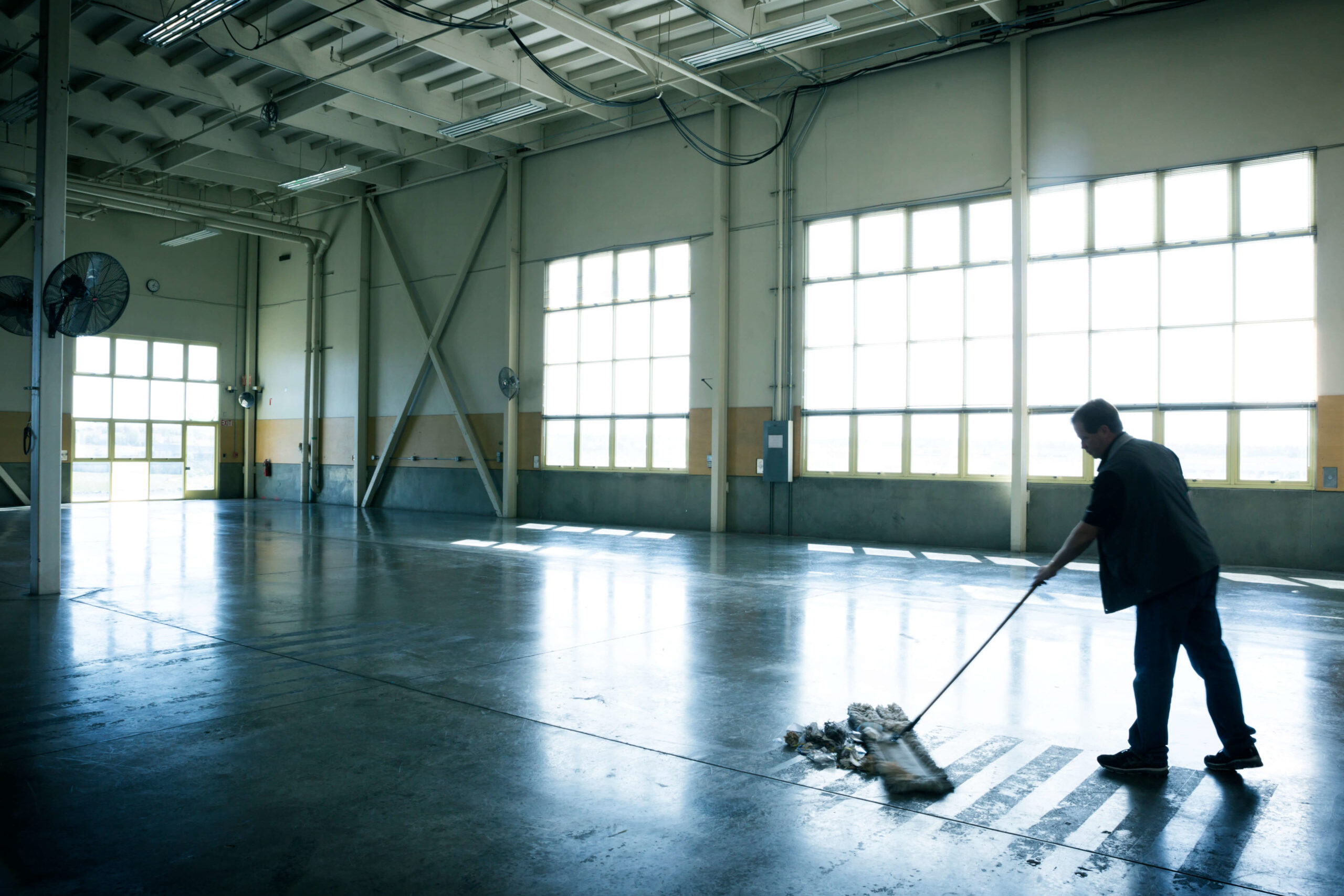
5S in the Japanese workplace – seiso: seeing, sweeping and shining (part 3 of 5)
Articles, Japanese business keywords
5S practices rooted in Japanese culture and customs
The success of Toyota’s manufacturing processes has brought 5S practices into the spotlight. These practices, often translated as Seiri = sorting, Seiton = organizing, Seiso = cleaning, Seiketsu = sanitizing and Shitsuke = sustaining, is a workplace methodology perfected by Toyota. In the previous two installments in this series of articles, we provided an overview of 5S and some ideas about seiri and seiton. Of the 5S practices, seiso = cleaning, is the most difficult for Japanese assigned to their companies’ factories in the US to explain to their American employees, perhaps because it is the most rooted in Japanese culture and lifestyle. To the Japanese, standards, methods and benefits of seiso are obvious. Here is an overview that helps explain the Japanese experience of seiso.
Seiso: the basics
In her book “製造現場の英語表現(Seizo gemba no eigo hyogen) (Effective Communication for Engineers),” Rochelle Kopp provides a concise explanation of seiso. “Cleaning. Shine and clean everything in order to spot hidden problems (oil leaks, water drops, etc.). Shine-clean it up.”
Seiso-(清掃)
Let’s look at how Japanese write seiso. The first character, 清 means “purify” or “cleanse.” The second character, 掃 means “to sweep.” Since Japanese live in very small houses, they prefer to sweep the entire house each morning to keep dirt and debris from living spaces. In addition, they remove their shoes before entering their homes to prevent contamination from the outside from entering.
Cleaning is learned and practiced at school
In Japanese schools, children are responsible for daily cleaning, beginning in first grade. Cleaning is performed at a set time each school day, usually after the lunch period, and typically lasts for about 20 minutes. Classes are divided into smaller groups to clean their assigned areas. They clean their own classrooms and common areas of the school, including the toilets. The groups rotate responsibilities for areas to be cleaned. Older students are expected to help students in lower grades learn how to clean. Custodial staff take care of repairs and emergency cleanup only.
This system creates a unified standard of cleanliness throughout the country. It teaches students that cleaning is everyone’s responsibility, and instills standard cleaning procedures. For example, students use cloths to clean floors. They do not use dust mops or long-handled tools as is typical in the U.S. Therefore, they are very close to the areas that they clean and see the dirt very clearly. After cleaning, cloths and washed, wrung out and stored in a prescribed method. Separation of the cloths used to clean floors and those used to clean desks is strictly enforced.
.
Cleaning is part of everyone’s job at the company
As with schools, cleaning is done by everyone in the organization, not just by janitors. Naturally, employees are expected to clean the areas and machinery that they regularly use. But they also clean common areas. They monitor general cleanliness and clean areas that need cleaning, even if they are not specifically assigned. They are taught to look at their workplace with fresh eyes—as though they were a customer dropping in unannounced.
By contrast, in many companies in the US, specialized staff do all the cleaning, even of individual desks and work areas. This is done at night when employees are not there. When employees return in the morning, the break room floor is shiny and the dust is gone from the window sills. Since this is the norm in the US, Japanese managers’ requests to clean up the workplace are often met with surprise.
The Japanese are also surprised. Unfortunately, to Japanese managers, especially those who are new to the U.S., this sounds like their stereotype of the American “It’s not my job” attitude. Don’t Americans understand that cleaning is part of every job? No job, large or small is complete unless the items used for the job are straightened up and all the tools put away in their proper places. Our work with Japanese managers involves helping them implement such a fundamental 5S practice given the differing attitudes towards cleaning between Japan and the US. ? We help them with the careful preparations required to implement successful seiso initiatives.
Benefits of seiso
Naturally everyone would like to come to work and have everything clean and well organized. Cleaning removes dirt and contaminants that might be harmful to employees. Dirt can hide problems such as cracks and poor fittings. Dirt can hide inefficient work processes and prevent their discovery.
Cleaning reveals defects and enables timely correction. This is why it is preferable for the same employees who use the equipment to be responsible for keeping it clean. Think of your clothing. Do you ever sit down at a meeting and notice a frayed cuff or a button missing on your shirt? If you iron your own shirts instead of pulling them out of a dry cleaner’s bag, you probably notice the wear and defects before others do. The same concept applies to the equipment used at work. Cleaning a machine flags abnormalities more effectively than simply operating it.
Well-implemented seiso programs also have long-term benefits when it comes to employee morale. Not only are workplaces cleaner and more efficient, but caring for equipment on a daily basis increases employees’ satisfaction with their contribution to the company. My neighbor who washes and waxes his car every weekend notices every dent, scratch and potential rust problem. His love for his car increases with the time and effort he spends caring for it. He probably enjoys his commute more than the rest of us.
Implementing seiso in the American workplace
We recommend to our Japanese clients that they work together with their American managers to develop seiso programs in a culturally-appropriate way. Systematic up-front preparation is essential to successful implementation. Work areas should be photographed prior to beginning the initiative. There must be an inspection method and a method of recognizing employee’s efforts. Seiso ideas must be presented to employees with opportunity for them to give their input and suggestions, and express their concerns. Employees must have the opportunity to request optimal cleaning supplies. When cleaning standards have been established for each area, cleaning and monitoring activities can be allocated. All this must be done before a single window sill is wiped! Jumping in too quickly to seiso activities can backfire without sufficient preparation and enforcement. After all, it is not a one-time fix. Seiso is like taking a bath. To be at all effective, it must be repeated on a regular, if not daily basis.
Seiso—cleaning to enjoy the workplace and discover hidden problems. Next month let’s look at Seiketsu (清潔), standardization of our 5S activities.
Related articles
Purpose should come from within, but also from outside Japan HQ
Recently an HR director for a Japanese financial services company in Europe told me that he had been
(Video) So, What is Monozukuri Actually?
Monozukuri is one of those well-known and often used Japanese words among people from outside of Jap
(Video) So, What is Ikigai Actually?
Ikigai - The Japanese word for the goal that gets you going - is often misunderstood by non-Japanese