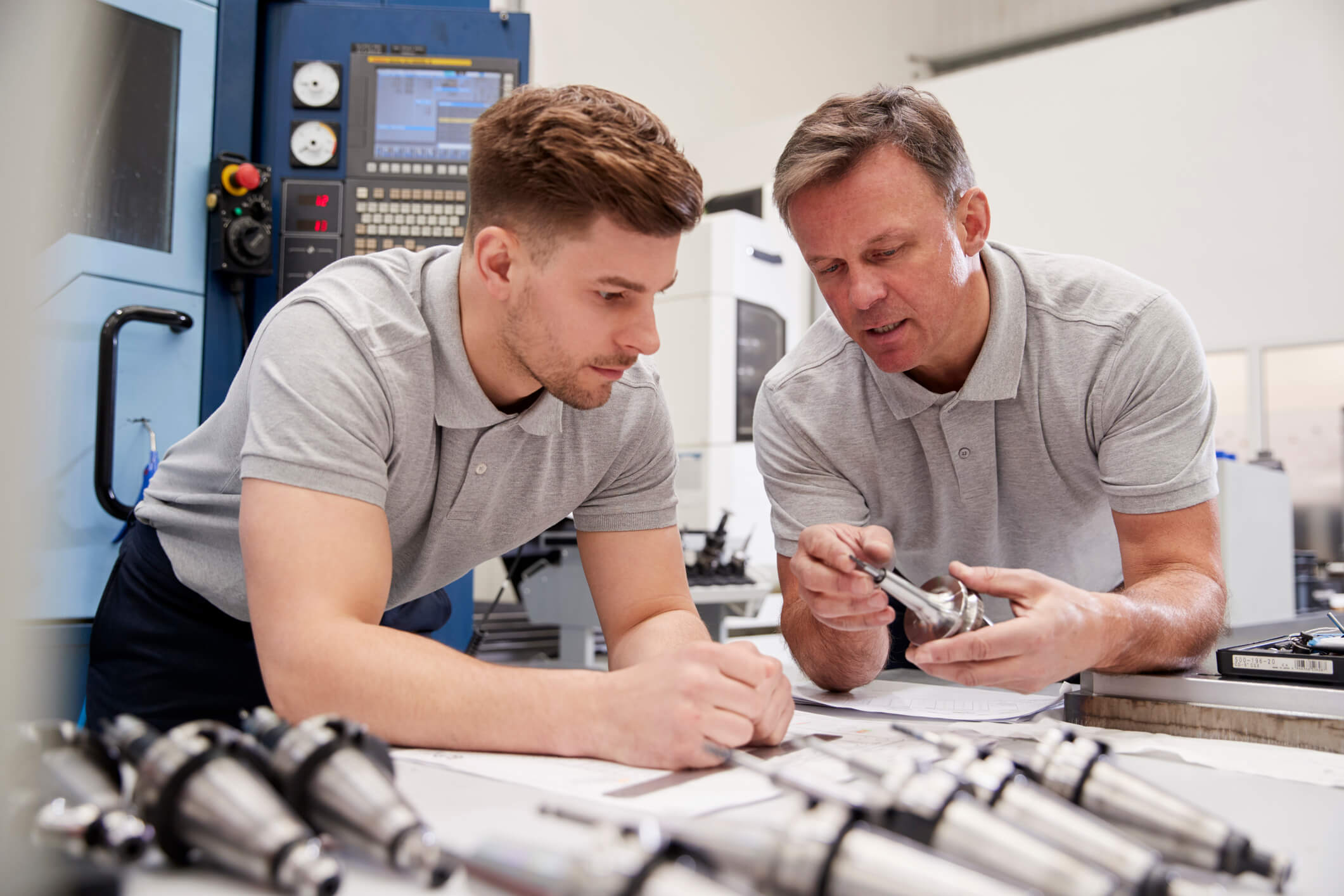
Jennifer Rosen, human resources manager at a Japanese companies’ manufacturing facility, is not having a good day. She has just received another resignation from one of the company’s engineers. This is the third such resignation she has received this month. The high turnover rate in the engineering department has become a chronic problem, and the President has specifically asked her to take measures to deal with it. He has told her “If it will help, offer them more money,” but Jennifer thinks that money alone won’t solve the problem. Thinking about the comments made to her by engineers exiting the firm, they seem more concerned about issues such as quality of life and feeling like part of the team. Some of the issues, Jennifer knows, have to do with the different styles between the American engineers and their Japanese counterparts. She knows that these issues are deeply rooted, and can’t be fixed by something as simple as a pay raise.
Sigmund Freud asked the famous question “What do women want?”, but for today’s technologically-based companies, the most important question seems to be “What do engineers want?” The answer seems just as confusing, when despite a companies’ best efforts engineers are so difficult to hold onto. The current labor market environment doesn’t make it any easier — job opportunities for engineers are plentiful, and the unemployment rate for certain types of engineers in certain geographic regions is actually negative. Yet it is imperative for companies to find ways to retain engineers, because they are essential to the success of technology transfer, research and development activities, and the proper functioning of manufacturing facilities.
Part of the answer to engineer retention lies in understanding the psychology of engineers, what they are really looking for in a job. The needs and expectations of American engineers are quite different from those of Japanese engineers, so Japanese companies in the U.S. sometimes have more than their fair share of challenges in engineer retention. This article will examine the attitudes and priorities of American engineers, with the intention of serving as clues to companies that want to effectively manage and retain them. It should be noted that many of the statements made in this article here are also true of other groups of highly educated white collar employees in the U.S., such as MBAs.
American Engineers’ Expectation 1: Elite treatment
One of the keys to understanding the mindset of American engineers is to look at the process of training that they go through. At most U.S. universities, admission to the engineering program is very competitive. Furthermore, engineering programs are known for their “weed-out” courses, tough classes designed to separate the wheat from the chaff. Attrition of those who can’t make the grade leaves those engineers who make it through the program feeling like an elite. They feel that their hard work — and high tuition amounts that they paid — entitle them to a special role in the working world. The way that corporations aggressively woo newly minted engineers and their high starting salaries tend to reinforce this mentality. However, several tendencies of Japanese companies run counter to these expectations.
Traditionally, Japanese manufacturing companies tend to emphasize equality, and tend to want to treat all employees the same — same rules, same benefits, same uniforms, etc. This often makes Japanese companies popular with blue collar workers, who welcome the egalitarian atmosphere. However, it runs the risk of alienating engineers, who believe that the education they worked so hard to achieve entitles them to be treated specially in some cases. Thus, having benefits systems, working hours, compensation schemes, workplace rules, and even uniforms that are the same for engineers as for production workers can sometimes lead to dissatisfaction among engineers.
Japanese customs concerning the role of newly hired employees can also be disappointing to the American engineer when he first joins the company. In Japan, what is learned in school is less important than hands-on experience. Newly-hired engineers start at the bottom, and are given basic or peripheral tasks (such as testing) that in the U.S. would be considered technician work rather than the work of engineers. The idea is that while doing these tasks they will watch and learn from their more senior colleagues. This works well in the Japanese context where humbleness, deference to elders, and apprentice-style learning are all valued.
In contrast, U.S. engineers have worked very hard specifically to earn the credential of engineer so that they can avoid technician-type work and do tasks which are more interesting to them. Even when they are first out of school, they expect to be assigned to projects which utilize the skills developed during their education. Thus, entry-level engineers will misunderstand when they are asked to do things that do not fit their definition of “engineering work.”
Suggested counter-measures:
• Hire sufficient technicians to handle technician-level work, so that it does not need to be assigned to engineers.
• Make an effort to give newly-hired engineers key project tasks and challenging assignments. Assume that newly-hired engineers are competent and capable ot handling important work right away. Respect the skills of younger engineers, and be careful that training does not come off as condescending.
American Engineers’ Expectation 2: At the Center of cutting-edge activity
One of the things that drives American engineers is the thirst for professional challenge — opportunities to use their skills on cutting edge issues, and to be an integral part of a company’s work.
In addition to the frustration caused by being asked to do technician-type work that seems peripheral to the main task at hand, many American engineers at Japanese firms are frustrated by the control that their Japanese colleagues hold over the engineering process. When crucial areas are handled by Japanese engineers stationed in the U.S., or by those based in Japan, American engineers feel that they are not at the center of what is happening. This feeling of being merely a helper is not appealing to high-performing engineering professionals.
Such concerns are further exacerbated when decisions are made by Japanese engineers, either among themselves or in consultation with colleagues in Japan, and not quickly transmitted to American engineers. In some cases, the American engineers may even continue with their work for a day or more before finding out that a change they didn’t know about means they have to backtrack and re-do work. Nothing is more irritating than the feeling of being out of the loop and wasting effort due to poor communication.
Crucial engineering documents, specifications, and design manuals which are only available in Japanese also make American engineers feel that they do not have access to important information. Reports, e-mails, and faxes that are written in Japanese are also frustrating, as is the inability to telephone counterparts in Japan who do not speak English. Social gatherings among Japanese engineers which do not include American colleagues can also be an irritant that contributes to the feeling of being left out.
Another issue that can make American engineers feel that they are not at the cutting edge concerns specific engineering approaches. Although of course Japanese engineering techniques are excellent, in some cases an American engineer may know of a more sophisticated or efficient technique for a given problem, based on their training or something learned at a previous employer. In many cases, there is a reluctance by Japanese companies to take such suggestions from American engineers, preferring to rely on the techniques that the company has been using in Japan. This lack of willingness to try something new and to listen to suggestions is extremely aggravating to American engineers, and makes them feel that the skills they bring to the table are not valued.
Suggested counter-measures:
• Involve American engineers in key meetings, and keep them informed of important decisions.
• Utilize a technical translator (either in-house or an external freelancer) to help manage the flow of technical information.
• Provide communications skills training to Japanese engineers to help them exchange information more effectively with American colleagues.
• Japanese engineers should be made aware that the style of engineering work and specific approaches are often different between Japan and the U.S. They need to value these differences and learn from what their American colleagues have to offer, rather than expect American colleagues to conform to a purely Japanese working style.
• Promote social interaction between Japanese and American engineers through company-organized social activities.
• Provide cross-cultural communications skills training to American engineers to help them interact more effectively with Japanese colleagues and get more involved in internal information flows and decision-making processes.
American Engineers’ Expectation 3: Good facilities and equipment
Any professional loves good equipment that helps them do their job better, and engineers are no exception. In fact, due to the nature of engineering, tools are particularly important. However, the corporate culture of many Japanese manufacturing facilities is one of austerity, and that often extends to engineering equipment. Having to share computers and plotters, using outdated hardware or software, working in an overly cramped environment cluttered with desks and papers — all these factors end up being everyday irritants. The spartan aura of many Japanese companies’ engineering workspaces is in sharp contrast to the spacious, comfortable, well-equipped facilities often provided by American firms.
Suggested counter-measures:
• Poll engineers to determine equipment, hardware, and software needs, and obtain budget to make necessary purchases.
• Place more emphasis on office environment and aesthetics.
American Engineers’ Expectation 4: Work/life balance
In Japan, it is not unheard of for firms to provide a room with cots so that engineers can sleep over at the company during crunch periods. While American engineers are also extremely dedicated to their jobs, they have different expectations about what sacrifices dedication to the company should entail. Many American engineers have the approach of working intensively during the day so that they can finish their work efficiently and go home at a reasonable hour. They are willing to put in crazy hours when there is an emergency, but not on a regular basis over an extended period of time.
This working attitude contrasts sharply with that of Japanese engineers, who tend to regularly put in long hours. This is partly due to work habits developed early in their careers, and partly due to the time difference between the U.S. and Japan. Since many Japanese prefer to keep their home a work-free zone, they tend to stay at the office late in order to make phone calls back to Japan concerning matters that need to be discussed. There is also more of a team camaraderie (or peer pressure) element in Japanese overtime — many Japanese find it difficult to extricate themselves from the workplace when their teammates are still working. Furthermore, in some cases Japanese engineers who are more familiar with the overall flow of the process will take it upon themselves to make sure that nothing falls between the cracks in the work being done by American colleagues. In such situations, the Japanese engineer will tend to just take care of the matter himself rather than asking for assistance, staying late to complete the task.
• De-emphasize face-time, and instead emphasize productivity. This should apply both to formal performance reviews and informal comments from managers to employees.
• Institute a flex-time system.
• Adopt a weekly no-overtime day that applies to everyone. Let the head office know about it too, so they won’t expect phone calls on that day.
• Encourage Japanese engineers to keep a better work/life balance. Both management and fellow employees should check with Japanese engineers to see if additional manpower support or pitching in could help them to reduce their overtime. Ensure that all necessary elements of the process are communicated to American staff who are involved.
• Communication with Japan should be done by fax and e-mail as much as possible, rather than on the phone.
American Engineers’ Expectation 5: Feedback and Recognition
Like other American professionals, American engineers crave positive feedback — a thank you or praise for a job well done. However, in Japanese corporate culture, such verbal expressions of appreciation are rare. This often leaves American engineers feeling that they are not valued.
• Train managers, especially Japanese ones, in positive feedback skills.
• Establish a system to publicly recognize and thank individuals and teams who have made significant contributions.
• Schedule festive events to celebrate accomplishments and thank the entire team for their hard work.
Assuming that a company also offers compensation levels that are competitive with what other firms are offering for similar work, addressing the issues raised above should help to increase engineers’ job satisfaction and improve their retention.
Related articles
Culture beats policies for sexual harassment prevention
I have noticed a significant increase in the numbers of Japanese companies asking me for support in
Which comes first, communication or values?
Several years ago, I developed a simple model to show how Japanese companies could built trust in th
Purpose should come from within, but also from outside Japan HQ
Recently an HR director for a Japanese financial services company in Europe told me that he had been